14-layer TU872 immersed nickel gold high frequency pcb board
Material: FTG-8250-0200
Layer Count: 14 layers
PCB Thickness: 1.6mm
Min. Trace / Space Outer: 3/3mil
Min. Drilled Hole: 0.25mm
Via Process: Tenting Vias
Surface Finish: Immersion nickel gold
High frequency PCB board, that is, high frequency circuit board, is a special circuit board designed for high electromagnetic frequencies. Generally speaking, when the frequency reaches or exceeds 1GHz, it can be called a high-frequency board
High frequency can be defined as a frequency above 1GHz. Its physical properties, accuracy, and technical parameters are very demanding, and it is often used in automotive anti-collision systems, satellite systems, radio systems and other fields.
Material selection standards for High frequency PCB board
High-frequency boards are mainly made of materials with high dielectric constant and low high-frequency losses. High-frequency boards are mainly made of materials with high dielectric constant and low high-frequency losses. Currently, fluorine-based dielectric substrates, such as polytetrafluoroethylene (PTFE, commonly known as Teflon), are widely used in high-frequency fields above 5GHz due to their excellent performance. In addition, FR-4 or PPO substrates are often selected and are suitable for products between 1GHz and 10GHz. The following is a brief comparison of the physical properties of these three high frequency substrates
High-frequency epoxy resin materials are mainly divided into three categories: epoxy resin, PPO resin and fluorine resin. Among them, the cost of epoxy resin has dropped, while fluorine resin has come second. Comprehensive dielectric constant, dielectric loss, water absorption, fluorine-based resin has the best performance and frequency characteristics, while epoxy resin is relatively attenuated. Especially when the product application frequency exceeds 10GHz, only fluorine resin printed boards can meet the demand.
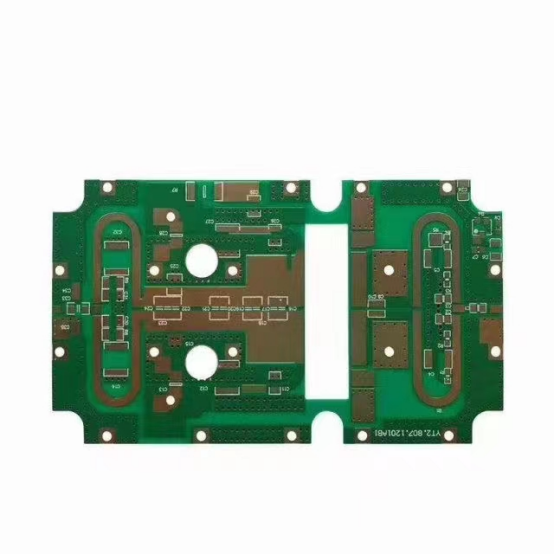
Basic characteristic requirements of high frequency PCB board materials
(1)The dielectric constant (Dk) should be kept at a low and stable level. Generally speaking, the smaller the value, the more conducive to the rapid transmission of signals. The rate of signal transmission is inversely proportional to the square root of the material’s dielectric constant, so a high dielectric constant may cause delays in signal transmission.
(2)Dielectric loss (Df) should be as small as possible, which is a key factor in ensuring signal transmission quality. The smaller the dielectric loss, the signal loss will be reduced accordingly.
(3)The thermal expansion coefficient should be as consistent as possible with the copper foil, because the inconsistency between the two will cause the separation of the copper foil during hot and cold changes.
(4)Water absorption should be kept at a low level, because high water absorption will affect the dielectric constant and dielectric loss when the material is damp, which will have a negative impact on signal transmission.
(5)In addition, other properties such as heat resistance, chemical resistance, impact strength and peel strength should also reach good levels to ensure that the high-frequency board can work stably under complex environmental conditions.
High frequency board production requirements and precautions
Drilling
In the drilling process, we need to pay attention to the following points: First, the drilling feed speed should be controlled to 180/S, and a new drill bit should be used, and aluminum sheets should be placed above and below. It is best to perform single PNL drilling to ensure that the hole No contact with moisture inside. Secondly, when passing the pore shaping agent, for the PTH hole sample, although concentrated sulfuric acid can be used, for safety reasons, we do not recommend this approach, and the processing time should be 30 minutes. Next, the production processes such as plate grinding, copper sinking, and wiring should be the same as normal double-sided panels. It is particularly important to note that there is no need to remove slag during the production process of high-frequency boards.
solder mask
In the soldering mask process, we need to abide by the following regulations: First, if the high-frequency board requires green oil for primer, it is prohibited to grind the board before soldering, and a red seal will be stamped in the MI to show the distinction. Secondly, if green oil needs to be printed on the base material, the printing should be done in two steps (to prevent the green oil from bubbling). The board must not be polished from etching to tin removal, and can only be air-dried. The first primer should be printed normally with a 43T screen and baked in sections. The temperature and time are 50 degrees for 50 minutes, 75 degrees for 50 minutes, 95 degrees for 50 minutes, 120 degrees for 50 minutes, 135 degrees for 50 minutes, and 150 degrees. Degree 50 minutes. After exposure and development, the plate can be ground, and then the second production can be carried out according to the normal process. It needs to be noted in the MI: Line film must be used for alignment for the first time. In addition, if some substrates need to be printed with green ink and some are not, a special “priming film” needs to be made, leaving only the part of the substrate that needs to be printed with green ink, and then proceed to the second normal production after priming the baking plate. It is particularly important to note that for substrates similar to 018092, if there is no need to print green oil on it, you only need to print green oil once to avoid that the green oil cannot be developed cleanly after the first priming.
spray tin
In the tin spraying process, the board needs to be baked before tin spraying at a temperature of 150 degrees for 30 minutes to ensure the tin spraying effect.
line tolerance
In terms of line tolerance, if there are no special requirements, the line width tolerance should be controlled within ±0.05mm; if there are special requirements, it will be made according to customer requirements.
Plate
In the selection of board materials, the specified boards must be used and strictly implemented in accordance with the requirements.