SMT mounting
- More than 10 years of placement experience
- No threshold
- No other fees
- No extension
choose us
One Stop/PCBA
From R&D and prototyping to small and medium-sized batches to large batches, starting from the design end, we provide a one-stop solution to customer pain points.
Fast Delivery
Prototyping production lines and batch production lines are flexibly equipped with controllable lead times and fast delivery.
Adequate inventory
Conventional resistance and capacitance sensors are always in stock and can be used directly to solve customers’ pain points of hard-to-find materials.
Quality Assurance
The core team has professional SMT industry experience, controllable quality, and one-stop service.
Patch introduction

PCB soldering services
Nissan Points: 5 million
PCBA production size: maximum 490 x 810MM
Plate thickness range: 0.1-6.5MM
Order quantity: 1-100000pcs
Electronic components: ① Passive components, minimum package 01005; ② The minimum pin spacing can be 0.25mm
Welding type: direct plug-in components (DIP devices) / surface mount components (SMT devices) / patch and plug-in hybrid / double-sided component welding (including patches and plug-ins)
Application areas: artificial intelligence hardware, communication equipment, automotive electronics, industrial control, security, medical, Internet of Things, etc.
SMT processing process
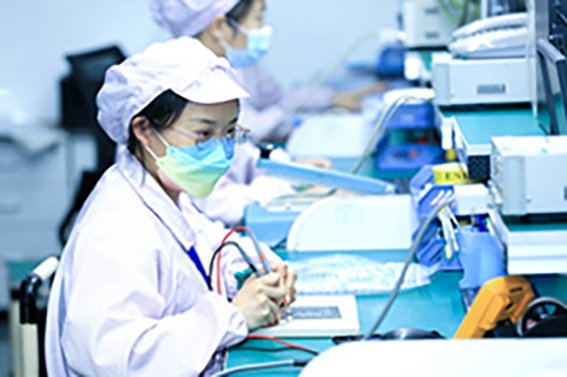
IQC test
Inspection purpose: to prevent online delivery delays caused by defective materials and poor manufacturing processes.
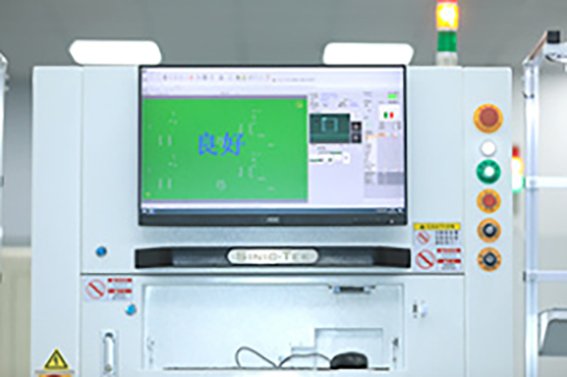
SPI detection
Inspection purpose: to discover in advance that the work in the previous process flows out of the next process Inspection standards: 3D inspection + data statistical analysis
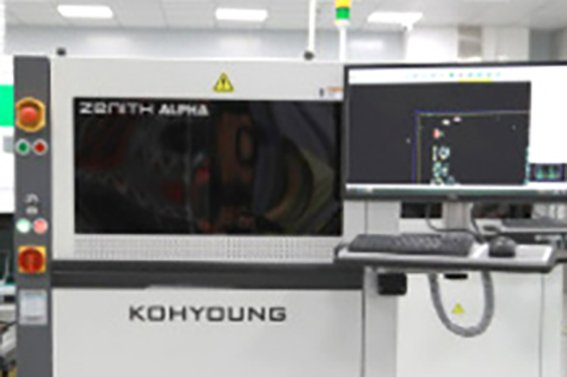
Online 3D AOI detection
Inspection purpose: Check whether there are errors, leaks, leaks, or defective materials flowing out of the produced products to the next process.

SMT first article inspection
Inspection purpose: To conduct a full inspection of the produced products to see if they are in compliance with the work instructions Inspection standards: process instructions for each product and instructions for each position
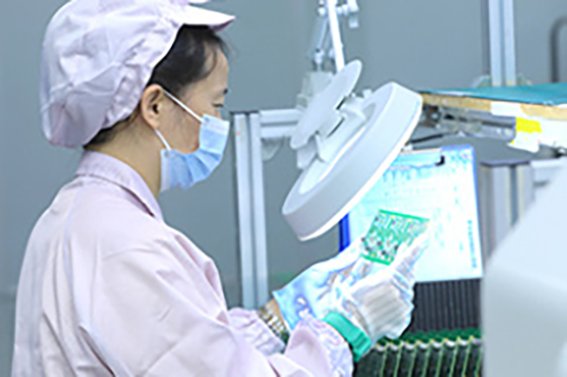
external assessment
Inspection purpose: To conduct a full inspection of the produced products to see if they are in compliance with the work instructions
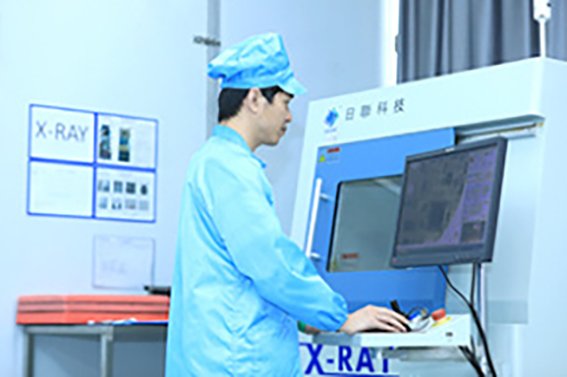
X-ray-welding inspection
Inspection purpose: To detect the solder joints of original parts that are invisible to the naked eye to avoid short circuits caused by false soldering and flow out of the next process. Inspection equipment: UFJ AX8200
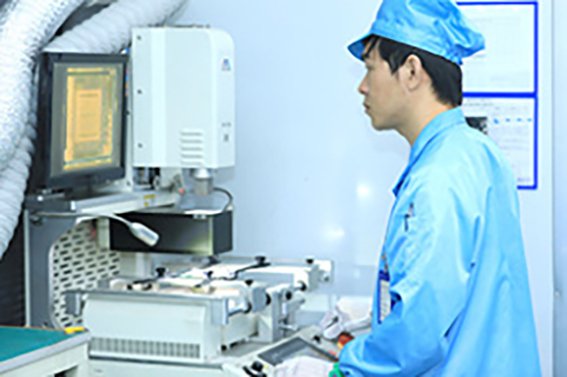
BGA device repair
X-ray detects BGA welding defects and disassembles and welds them under temperature-controlled conditions to slow down the impact on the device and ensure the quality of repair welding

QA testing
Standardize the inspection of shipped finished products to prevent unqualified products from being shipped Anti-static packaging and safety protection warehousing and delivery